The metal aluminum is an integral part of our daily lives. Across the globe, aluminum has been used for almost 200 years. In the 19th century, shortly after it was first extracted from ore, aluminum was used in tanning, dyeing fabrics, and fireproofing.
Not too long afterward, this element’s unique properties saw it used in power transmission lines. One of the first Wright brothers’ biplane engines was pieced together with aluminum. By the time World War II was in full swing, aluminum was used to build aircraft bodies and ship parts.
Usage of aluminum in the astronautics industry began in the 1980s when used to construct aluminum oxide rocket boosters. Now aluminum is being used to make alloys for space vehicles. The metal’s usage in constructing air batteries has enabled car makers to create vehicles that run longer on a single charge. This technology may be used to power space vehicles.
So, what made aluminum the go-to metal for the manufacture of aerospace technologies?
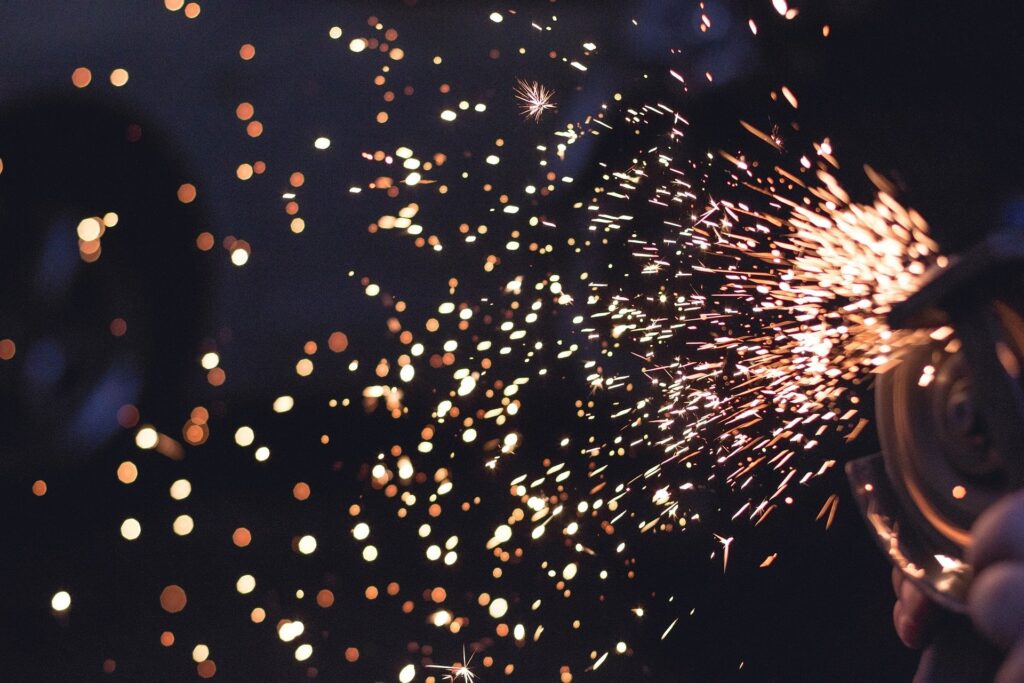
Aluminum Characteristics
- Cost: The cost of aluminum is the reason its use has not been so widespread. But one of the ways it can be a cost-saver is that it can be fully recycled.
- Lightweight, high strength: Anyone in professional racing will be quick to point out aluminum’s utility in making high-performance engines. Pistons, wheel spindles, and other engine parts in racing cars are made from aluminum because of their strength and lightness. The less weight a vehicle has to drag, the quicker it will be. This is the same reason why aircraft engine parts are also forged from aluminum.
- Durability and corrosion resistance: One of the key reasons aluminum is the preferred metal for aerospace machinery is its corrosion resistance. Conditions in outer space are not as forgiving as they can be here on earth. Space stations can be in orbit for upwards of 20 years. Building their components using a metal known for its durability therefore only makes sense.
- Recyclability: Almost 75 percent of the aluminum ever produced on the planet is still in use today. This speaks volumes of the metal’s recyclability. Aluminum recycling has been going on since the early 1900s when it was discovered the metal is 100 percent recyclable and will retain its properties indefinitely. Using recycled aluminum makes sense for our beloved planet’s life and the profitability of businesses. Recycling aluminum uses 95 percent less energy than extracting it from its primary source.
Forging Capabilities
In closed-die forging, there are a pair of die with impressions of the desired object. These are brought together to form the object by either a mechanical, hydraulic, or upsetter press. The beauty of closed-die forging is that it can create virtually any type of object of virtually any size you wish to have. And after it is produced, it will require minimal finishing to get it to a usable state. This makes this process well suited to an aluminum forging manufacturer for aerospace industries creating those intricate but hardy parts required for engine components.
The forging process itself, outside of aluminum’s qualities, contributes to the strength and durability of the part produced. This is because of the quality of the internal grain structure formed from the process. The metal produced will also be of low density, making it ideal for aircraft-grade parts production.
Alloys and Applications
There are several aluminum grades, each of which is useful in making different parts of space-bound aircraft.
- 2024: Used to make the structure of such aircraft. It is also used in the restoration and repair of aircraft.
- 3003: Used in the creation of baffle plating and cowls.
- 5052: Has the corrosion-resistant qualities that make it ideal for use in making fuel tanks.
- 7075: This grade of aluminum is usually alloyed with other metals to strengthen the structure of aircraft.
Having mentioned alloys, here are some of the aluminum alloys that are specifically made for the aerospace industry:
- 2000 Series: Used where strength and resistance to high temperatures are required. It consists of aluminum alloyed with two to 10 percent of copper.
- 6000 Series: This alloy is used where strong but malleable metals are required. It gets these qualities by alloying aluminum, magnesium, and silicon. This series is used to manufacture more intricate parts and fittings such as hydraulic pistons and couplings.
Discover Aluminum
If you’re about to embark on an aerospace project and require to create components that will withstand the rigors of outer space, aluminum is your best bet. However, it is wise to take time to get as much information about this metal as you can. It is expensive, and you don’t want to invest handsomely in something that is not suited to the purpose.